Welding WPS: Typical Errors to Avoid and How to Correct Them
Welding WPS: Typical Errors to Avoid and How to Correct Them
Blog Article
Mastering Welding WPS Specifications: Ideal Practices and Techniques for High Quality Welds
In the realm of welding, grasping Welding Treatment Requirements (WPS) standards is an important component that directly affects the high quality and integrity of welds. As we browse with the details of welding WPS requirements, discovering crucial insights and strategies for achieving top-tier welds will be vital for welders looking for to excel in their craft and create welds that stand the examination of time.
Comprehending Welding WPS Specifications
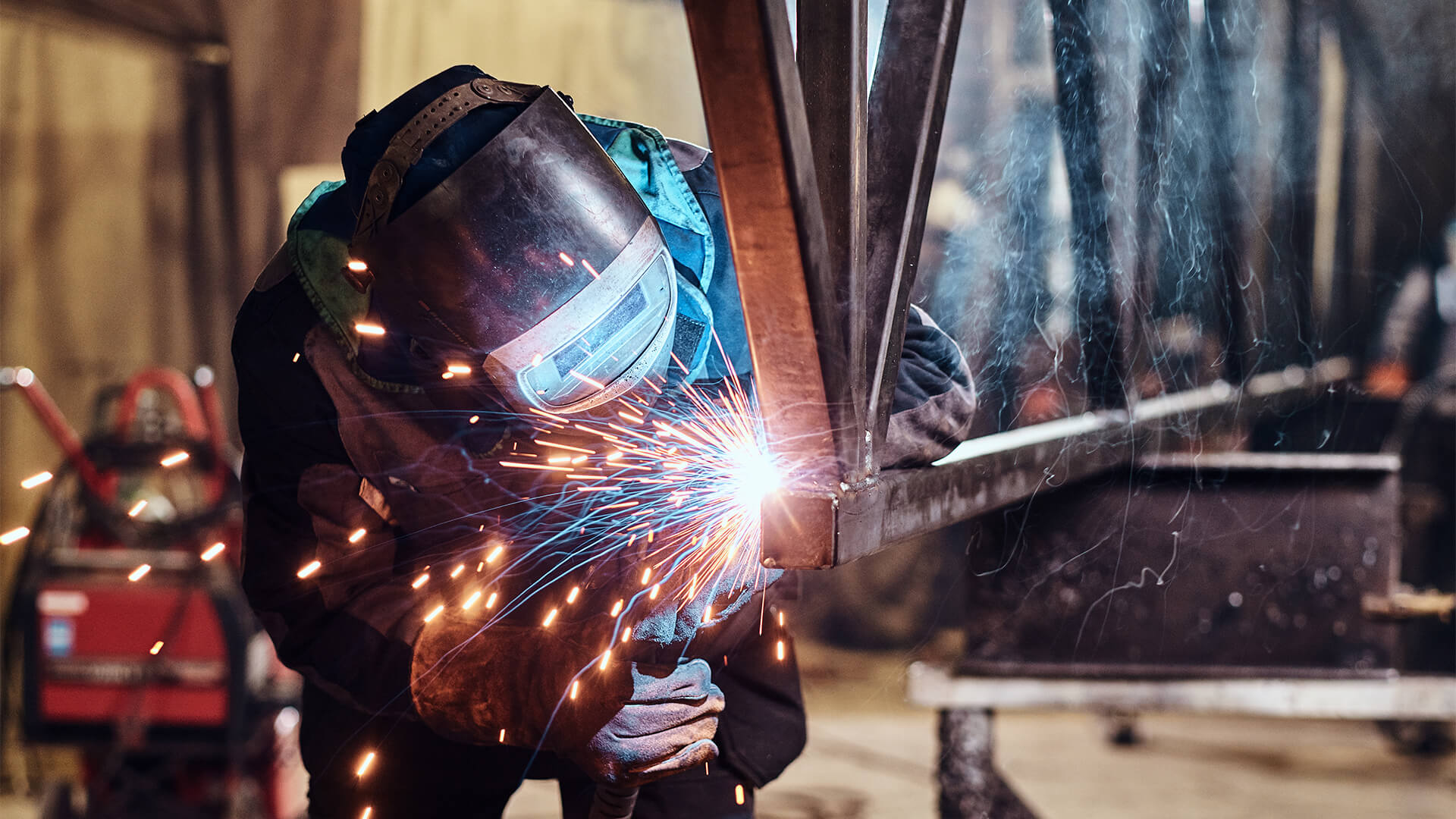
Understanding WPS requirements is important for welders, engineers, and examiners included in welding procedures. By adhering to WPS standards, welders can create welds that meet the required mechanical homes and architectural honesty. Examiners depend on WPS paperwork to validate that welding procedures are being followed properly which the resulting welds are of premium quality. Designers make use of WPS requirements to make welding treatments that ensure the sturdiness and integrity of welded structures.
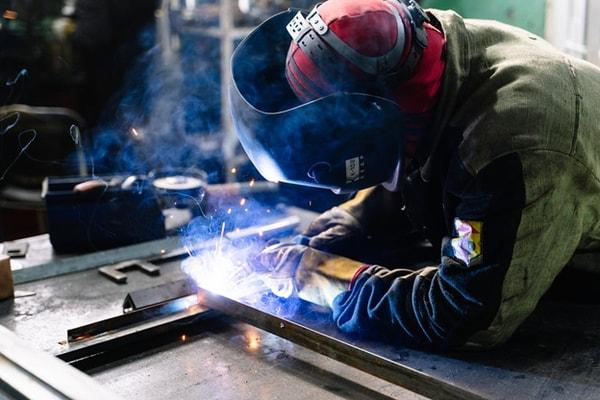

Necessary Tools for Top Quality Welds
Grasping welding WPS standards is necessary for welders to properly utilize the vital tools needed for creating top quality welds. The type of welding device needed depends on the welding procedure being made use of, such as MIG, TIG, or stick welding. Cord brushes and damaging hammers are vital for cleansing the weld joint before and after welding to remove any type of impurities that can influence the top quality of the weld.
Key Methods for Welding Success
To attain welding success, one have to master the crucial techniques vital for generating high-quality welds. Keeping a stable hand and a secure welding placement throughout the process is essential to attaining precision and uniformity in the welds. By grasping these crucial strategies, welders can raise the click this site quality of their job and achieve welding success.
Ensuring Conformity With WPS Criteria
Moreover, welders need to undergo training to acquaint themselves with the WPS standards relevant to their work. Normal audits and inspections must be carried out to verify that welding tasks line up with the suggested WPS standards. In addition, maintaining thorough documents of welding parameters, devices calibration, and inspection outcomes is vital for demonstrating compliance with WPS requirements - welding WPS. By diligently adhering to WPS requirements, welders can make sure that their work satisfies the necessary high quality levels and adds to find out the overall success of the welding project.
Troubleshooting Common Welding Issues
To address this, guaranteeing proper cleaning of the base metal before welding and making use of the right protecting gas can significantly minimize porosity. Additionally, distortion, breaking, and spatter are usual welding obstacles that can be alleviated with correct joint prep work, constant warm control, and choosing the proper welding consumables. By extensively comprehending these usual welding concerns and their root causes, welders can successfully troubleshoot issues and attain high-grade welds.
Verdict
In conclusion, understanding welding WPS requirements requires a comprehensive understanding of the guidelines, using crucial tools, and implementing essential methods for effective welds. Making sure compliance with WPS standards is critical for creating quality welds and preventing typical welding concerns. By complying with ideal strategies and methods, welders can accomplish dependable and constant outcomes in their welding tasks.
In the realm of welding, understanding Welding Treatment Specification (WPS) standards is an essential element that directly influences the quality and integrity of welds.When delving into the realm of welding techniques, a vital facet to comprehend is the value and ins and outs of Welding Treatment Specification (WPS) criteria. WPS requirements give an in-depth standard for welding operations, ensuring uniformity, quality, and security in the welding process. The kind of welding device needed welding WPS depends on the welding procedure being utilized, such as MIG, TIG, or stick welding.Attaining welding success via the proficiency of key methods requires a detailed understanding and adherence to Welding Procedure Specification (WPS) standards.
Report this page